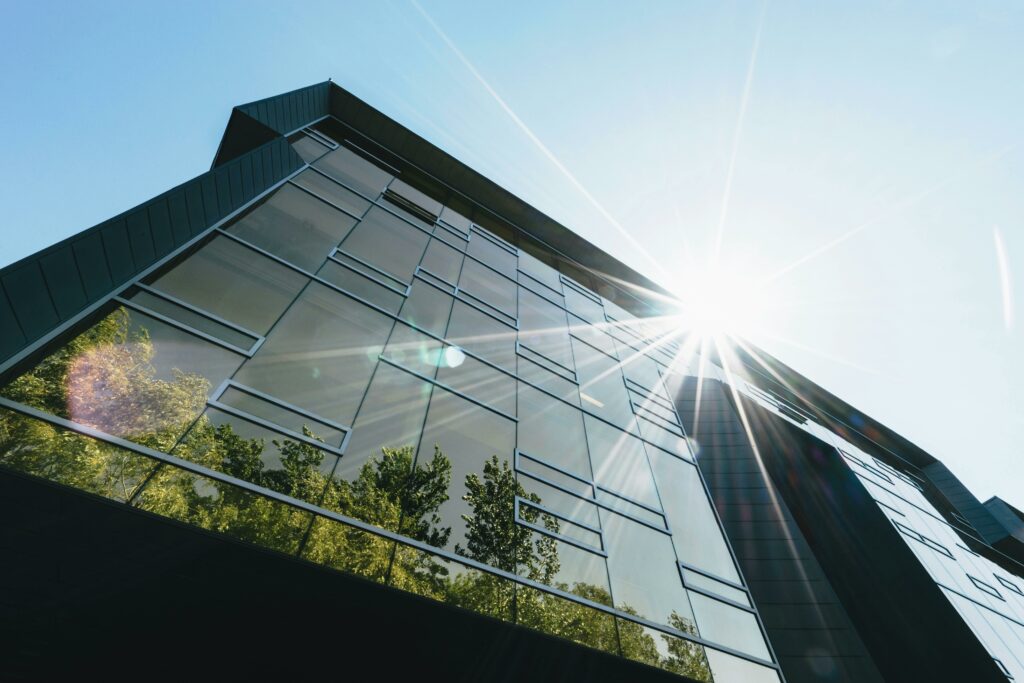
Buildings are not just the occupiable space within them; they are repositories of valuable materials, ready for reuse. Yet today, most of that value is lost as materials are sent to landfill instead of being sent onwards to a next life. Can technology, policy, and practical action change that?
The construction industry is responsible for nearly 40% of global carbon emissions, with 11% stemming from the extraction, processing, and use of virgin materials. As urbanisation surges, equivalent to adding a city the size of Paris every day, the industry’s linear approach of “extract, use, discard” is becoming increasingly unsustainable.
Yet, many structurally sound materials are discarded once they leave a site, as their practical reuse value is overlooked. I first became fascinated by material reuse in construction in 2021 after attending a talk that laid out the stark energy intensity of recycling and introduced me to the concept of high-value reuse, using materials again in the same way, with minimal alterations.
As a structural engineer, I reflected on the buildings I had worked on, some dating back to 1810 and realised that materials remain useful as long as they stay in place. But once removed, they are too often dismissed as unusable and processed as waste, rather than recognised for their potential. Why does it work like that? This question has driven my work ever since.
Reusing materials is not a minor intervention, it delivers carbon savings of 80% to 97% compared to new materials, making it one of the most impactful strategies for reducing embodied carbon in construction. The barriers preventing the shift to using reclaimed materials over new are largely logistical, not scientific, meaning they can be overcome with the right technology, policies, and industry mindset.
Material reuse is not a new concept. For centuries, cities have been built from the remnants of the past, sometimes out of necessity, sometimes for aesthetics, and sometimes as a display of power. But today, reuse must evolve beyond historic precedent into a structured, scalable approach, one that is enabled by technology and integrated into modern workflows.
Throughout history, reclaimed materials have shaped the built environment. The Colosseum in Rome was stripped of travertine blocks and iron clamps, which were repurposed into St. Peter’s Basilica and Palazzo Venezia. After World War II, London relied on reclaimed bricks to rebuild bomb-damaged infrastructure. St Albans Cathedral was constructed using bricks from Roman Verulamium, blending styles while preserving history. And in 1204, materials looted from Constantinople were incorporated into St. Mark’s Basilica in Venice, not just for reuse but as a statement of cultural dominance.
While motivations for reuse have shifted over time, the core principle remains: materials retain value beyond their original use. The challenge today is no longer whether reuse is possible, it is how to make it scalable, efficient, and an industry norm rather than an exception.
The role of technology: Unlocking efficiency and transparency
The most influential sustainability choices happen before construction even begins. Optioneering, which evaluates multiple design scenarios to optimise sustainability and efficiency, helps determine whether a building can be retained and adapted instead of being demolished. Keeping as much of the original asset as possible often reduces embodied carbon, making refurbishment a more sustainable choice whenever feasible. Whole life carbon assessments provide data-driven comparisons, allowing designers to quantify and compare the sustainability impact of different design options, strengthening the case for reuse where viable.
To enable material reuse at scale, designers and contractors need accurate data on what exists within buildings today. In some countries auditing existing buildings for material reuse is mandatory, ensuring valuable resources are identified before demolition. Technologies like 3D scanning and QR-coded inventories streamline this process, enabling materials to be efficiently catalogued and either reused within the project or resold. AI-powered platforms are also making waste tracking more effective through real-time monitoring, automated data capture, and predictive analytics.
Without financial incentives, procurement requirements, or enforceable reuse targets, developers have little economic or regulatory motivation to prioritise reuse over demolition
While these tools focus on existing buildings, material passports are enabling the future reuse of new buildings. Currently used to store data about newly installed materials, they create detailed records of materials, tracking location, geometry, demountability, and embodied carbon footprint. By embedding this data into new projects from the outset, material passports ensure that today’s buildings become material banks for the future, making reuse easier in the next cycle of construction.
Beyond platforms: innovations driving sustainable materials and reuse
New sustainable materials and mechanised processes are helping shift the industry away from carbon-intensive materials. 3D-printed construction is gaining traction, with projects like ICON’s 3D-printed communities in Texas and the MX3D steel bridge in Amsterdam showcasing its potential. Modular construction, as seen in the Dyson Institute Village’s use of cross-laminated timber (CLT) pods, offers a low-waste, prefabricated alternative to traditional building. Meanwhile, waste-derived materials like K-Briq (bricks made from nearly 100% recycled demolition waste) are redefining resource efficiency, while bio-based materials such as MykoSlab (mycelium-based insulation) provide naturally regenerative alternatives. While adoption remains niche, these innovations signal a growing shift toward scalable, circular solutions.
Policy and regulation: Global momentum, uneven implementation
Legislation is gradually catching up, but gaps remain. The EU will mandate embodied carbon reporting by 2028, expanding to all projects by 2030. Some countries, like the Netherlands, France, and Denmark, have policies promoting material reuse, but enforcement varies. In the U.S. and Canada, progress is fragmented, with state and city-level initiatives rather than national policies.
Many regulations fail to distinguish between reuse and recycling, despite reuse offering significantly greater carbon savings. For instance, while the EU’s circular economy strategy promotes material efficiency, much of its regulation focuses on recyclability rather than direct material reuse.
Without financial incentives, procurement requirements, or enforceable reuse targets, developers have little economic or regulatory motivation to prioritise reuse over demolition. Until policies move beyond broad circularity goals to mandating and mainstreaming material reuse, it risks remaining a niche practice rather than an industry standard.
The power of practical action: the role of doers on the ground
While policies and digital tools are advancing material reuse, much of the momentum has come from bottom-up efforts led by contractors, practitioners, and material reuse services. A clear example of this is the work of David Bennink, also known as “Deconstruction Dave”, who founded the Building Deconstruction Institute to train professionals in deconstruction and material reuse. His efforts have helped expand deconstruction practices across 44 U.S. states, four Canadian provinces, and nine other countries.
These grassroots efforts are now influencing large-scale projects. Despite initially focusing on smaller-scale timber-framed housing, Bennink’s expertise in practical deconstruction strategies led to his firm, Re-Use Consulting, being selected as the deconstruction and circularity consultant for SPARC Kips Bay, a $2.1 billion redevelopment project. This long-term initiative, still in its early stages, involves the careful dismantling of an 800,000-square-foot complex. While the full impact is yet to be realised, it highlights how hands-on expertise in reuse is influencing large-scale urban projects.
The industry stands at a tipping point. The solutions exist, the momentum is building, and the need is undeniable
Contractors are no longer just tearing down buildings; they are engineering the future of deconstruction. Denmark’s Gamle Mursten automates mortar removal from salvaged bricks, while Quebec’s Brique Recycmachine cleans bricks on-site, reducing costs and waste. Urban Machine uses AI-driven scanning alongside a disassembly line to assess, process, and prepare reclaimed timber for reuse, removing fixings and verifying quality – eliminating key barriers to reuse at scale. This shift is being driven by practitioners on the ground, finding ways to make material reuse both practical and scalable.
Projects like Holbein Gardens, one of the UK’s first major steel reuse projects, prove that reuse is viable at scale, reclaiming 24 tonnes of steel and achieving 35 tonnes of carbon savings. If reuse can work for structural steel, what other materials might follow? Could we extend these principles to drive reuse across the entire industry?
Why the future requires all three
No single solution will drive sustainable construction at scale. Technology, policy, and practical action must work together – technology provides the tools to enable reuse, policy creates the mandates to require it, and practical action proves that it can be done. But if any one of these pillars falls behind, reuse will remain sporadic rather than standard practice.
At re:new, we are scaling reuse by educating the industry on methodologies, showcasing real-world applications, and connecting reuse services with projects, making circularity both accessible and achievable.
Breaking down barriers together
The groundwork is laid, but achieving circularity at scale requires a bold shift. Digital tools must move beyond pilot projects to become industry standards, policies must evolve from recommendations to enforceable mandates, and contractors must be empowered to lead innovation on the ground. Without this collective momentum, sustainable construction will remain a niche rather than the norm.
The next step is scaling solutions globally. Technologies hold the potential to make reuse accessible at scale, but governments and businesses must commit to ensuring that circular construction is not an afterthought, but a fundamental industry practice.
Sustainable construction cannot rely on isolated projects; it demands cross-sector collaboration, regulatory backing, and industry-wide commitment. The challenge is no longer can we do it, but will we do it at scale?
The industry stands at a tipping point. The solutions exist, the momentum is building, and the need is undeniable. The choice before us is clear: will we continue down the unsustainable path of waste and over-extraction, or will we seize this moment to transform how we build for the future?
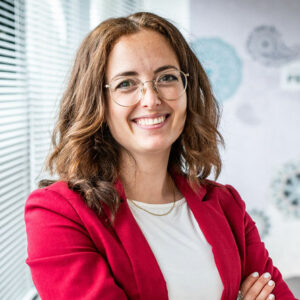
Saskia Manson
Saskia Manson is Founder of re:new, Sustainability Consultant and beVisioneers Fellow