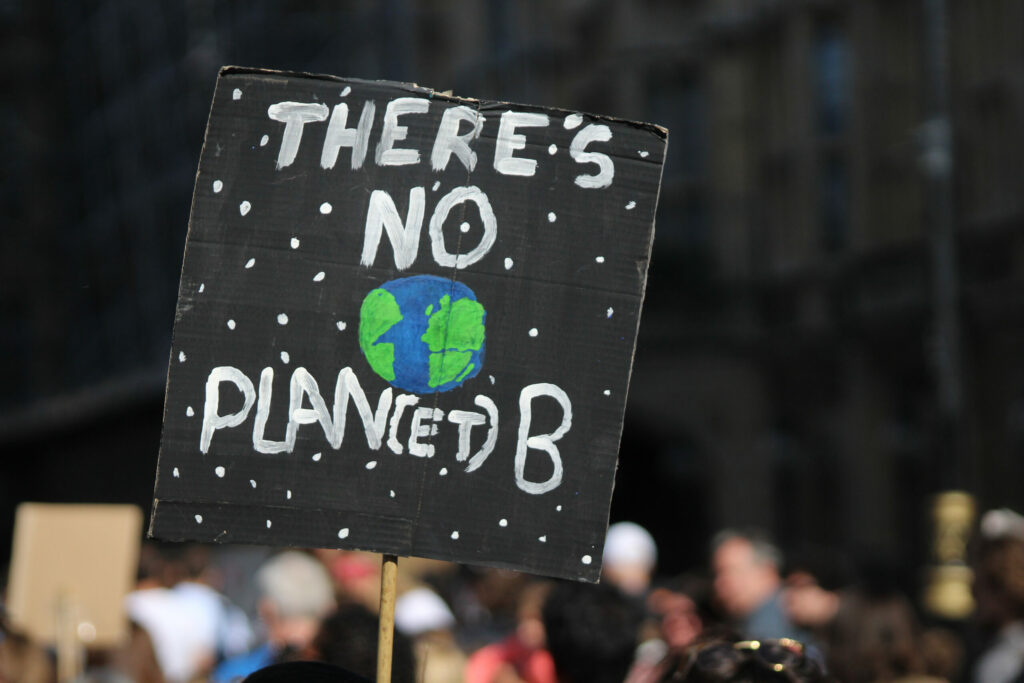
Plastic is a major contributor to the climate crisis, but it isn’t irreplaceable. Tom Van Aken, Avantium’s CEO, talks to Tech For Good about the 100% plant-based, fully renewable plastic that might move the industry away from fossil fuels
Warm winters, wildfires and hurricanes have shown that the climate crisis is no longer a feared possibility – it’s the present.
Despite the commitments by various nations to cut coal emissions, reverse deforestation and make grand investments in clean energy, there is still no sign f a grand-scale plan to target climate change globally. But, as the leaders of the world debate how to reduce global emissions, some organisations are already taking on one of the most polluting materials out there: plastic.
Globally around 300 million tonnes of plastic is made from fossil fuels every year. In 2018, it was reported that the chemical industry is responsible for 8% of global human-derived GHG emissions, along with the warning that this could rise to 15% by 2030 and 25% by 2050. Although there is a general global consensus on the need to move to a 100% renewable and decarbonised energy sector, there is not yet an equivalent strategy for the chemical and plastics industry, where carbon is the essential element.
The path towards sustainable plastic is a long one. And one in which organisations, governments and private individuals all have a role to play.
“The future of plastics is above the ground, so we need to wean the world away from petroleum,” says Tom van Aken, CEO of Avantium. “In order to move to renewable carbon, we need truly innovative technologies. We also need to set up completely new supply chains. This means rethinking the chemical and plastics industry, carefully balancing and weighing sustainability, performance and costs. Businesses need to take an integrated approach and implement practices that can lead to genuine change on environmental issues while ensuring their commercial goals are still being met.
“I strongly believe that businesses have a key role to play in solving the world’s climate crisis. Companies can set examples for their industry peers to follow and spark a chain reaction that can have a tangible, positive impact. By working together with other companies, governments and institutions, we can create more sustainable practices that will reduce environmental impact and make the world a greener place for future generations to enjoy.”
“The future of plastics is above the ground, so we need to wean the world away from petroleum,” says Tom van Aken, CEO of Avantium. “In order to move to renewable carbon, we need truly innovative technologies. We also need to set up completely new supply chains. This means rethinking the chemical and plastics industry, carefully balancing and weighing sustainability, performance and costs. Businesses need to take an integrated approach and implement practices that can lead to genuine change on environmental issues while ensuring their commercial goals are still being met.
“I strongly believe that businesses have a key role to play in solving the world’s climate crisis. Companies can set examples for their industry peers to follow and spark a chain reaction that can have a tangible, positive impact. By working together with other companies, governments and institutions, we can create more sustainable practices that will reduce environmental impact and make the world a greener place for future generations to enjoy.”
Avantium is a company taking these challenges head-on. Its vision is simple, but not easy: to achieve a fossil-free chemical industry by 2050.
Avantium’s mission would mean turning the chemical industry on its tracks and promoting a 180-degree shift towards renewable carbon. To achieve this, the company has developed polyethylene furanoate (PEF), a new type of plastic made from sugars. This “new generation polyester” is 100% plant-based, fully recyclable and has a significantly lower carbon footprint than traditional plastic, while also maintaining all its benefits. The material is created through a new technology called YXY, capable of converting plant-based sugars into furandicarboxylic acid (FDCA), the key building block for a wide range of plant-based chemicals and plastics. Avantium has successfully demonstrated the YXY Technology at its pilot plant in Geleen, the Netherlands.
“Plastics are everywhere and have ideal properties for packaging solutions: they are light-weighted, transparent and produced in a low-cost manner,” Van Aken says. “The downside of today’s plastics is that they are made from petroleum and contribute to carbon emissions and that they pollute our natural systems after they have been used. Our solution is to address these problems while making sure that we don’t sacrifice on performance.
“Plastics do not need to be made from fossil feedstock: we are making them from plant-based sugars. Rather than try to do the impossible of completely moving away from plastics, we wanted to create a realistic, but sustainable solution that can be adopted on a mass scale. We believe that PEF will ultimately become mainstream once global production through large-scale licensing is achieved.”
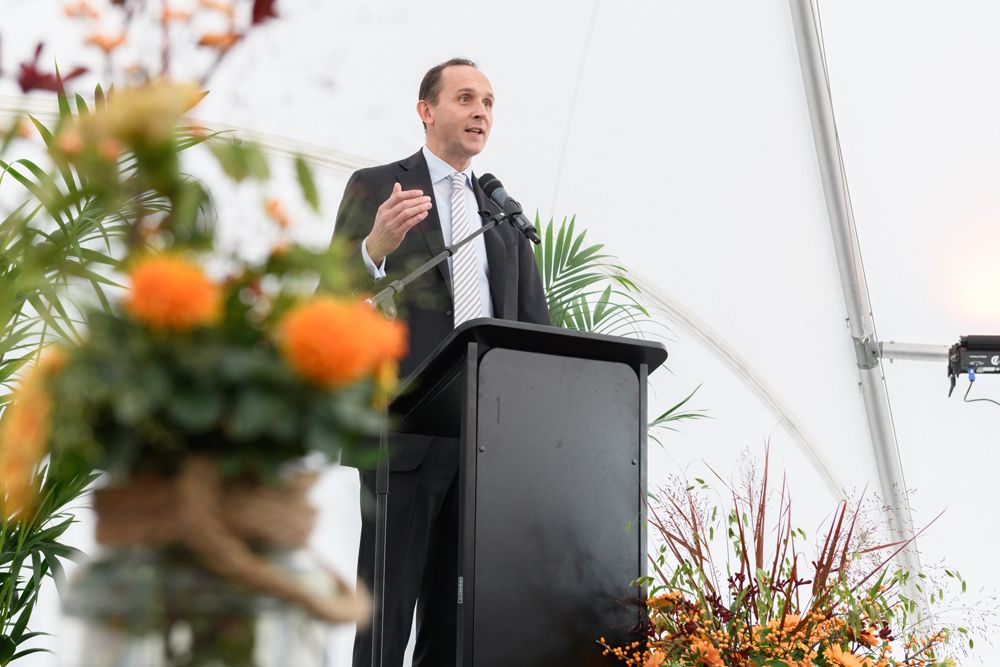
It has been decades since a new product has been introduced into the plastics industry, a difficult one to enter into, particularly when trying to compete on pricing. Van Aken predicts that, although PEF will initially be more expensive than traditional plastics during the first phase of market entry, the performance of the product and its environmental advantages will overcome those initial barriers until higher production volumes can be achieved and the cost can be reduced.
“PEF’s clear advantages in increasing the shelf-life of food and beverages, reducing waste, all while using less material, justifies the initial higher price,” Van Aken says. “In the long-term, we believe that the costs of producing PEF will come down when we scale up and further optimise the technology.
“Our technologies have potentially transformational applications and can help wean the world away from fossil-based resources, accelerating the transition to a fully circular economy.”
Materials like PEF have the potential to forever change packaging, textiles, film, and many other consumer products. They address one of the main problems of replacing plastic with paper, as it can be used to package food and drinks, including the carbonated ones – which are notoriously hard to package – as well as cosmetics. Overall, PEF provides a longer shelf-life of packaged products, therefore avoiding unnecessary food and product waste.
PEF can be used as a single layer in small bottles for soft drinks, beer and juices, replacing glass bottles, aluminium cans and multilayer bottles. However, it was not enough that PEF is made from sustainable materials. In order to address the challenges of global warming, it also had to be recyclable itself, to avoid creating more waste.
Small steps are being taken, such as events like COP26, but leaders need to understand we need radical change to hit the proposed timelines. Ultimately, we are running out of time
Currently, most of the plastic bottles that are used for packaging are made from polyester, also known as polyethylene terephthalate (PET). However, many multilayer PET bottles include polyamides (PA) such as MXD6 for barrier properties. This creates a challenge when it comes to recycling, as PA has a very low compatibility with PET, making it essential to sort out the PA from the PET in the recycling stream. In contrast, PEF can substitute polyamides as barrier material in multilayer PET bottles, enabling the recycling process of these packaging solutions in combination with PET.
“It was important for us to make a polymer that can be processed in existing recycling streams and can be recycled alongside PET,” Van Aken says. “With similar chemical properties to PET, both can even be recycled together. PEF is compatible with PET mechanical recycling assets, and when processed as part of the PET recycling stream, it has been proven that PEF has a much lower environmental impact than other barrier materials. Moreover, PEF products can also be recycled entirely by themselves in a closed-loop system.”
PEF can also degrade much quicker than PET. An accelerated study on industrial compostability by OWS in Gent, Belgium has shown that PEF degrades to CO2, water, and biomass in 250-400 days at 58 degrees in soil. By comparison, PET is estimated to take between 300 to 500 years to break down
“While it is ideal that PEF is recycled or reused again until the end of its lifecycle, should it unintendedly end up in nature, it will help reduce the endless plastic accumulation,” Van Aken says. “But let us be very clear: this is not a permission to litter, PEF is a high-quality polymer designed for recycling.”
One concern that comes with using sugar-based products is its impact on the agricultural sector. Food scarcity is already a huge problem in certain countries of the world, and with the constant increase in global population, it is one that will need to be addressed soon.
To avoid creating a bigger problem than the one it solves, PEF uses plant sugars from sugar beet, corn or wheat as feedstock, or convert non-edible biomass such as agricultural and forestry waste streams. By using waste from sustainable forestry management and agriculture and turning it into high-value materials, Avantium is further supporting waste-management initiatives and ensuring that the whole of PEF’s supply chain is sustainable.
“We don’t want our products to compete with food supply chains,” Van Aken says. “Creating bioplastics from renewable sources and plant-based feedstock can be managed in a very sustainable way and shouldn’t be in competition with food production. In fact, increased demand for non-food applications could support a healthier agriculture sector and stable food supply through investments towards higher yields, sustainable land-use practices, and secure supply.”
“We never really stopped,” says Balfour. “We started running this in 2019 and we are still going now. A new promotion has just gone live in Tesco in the UK. So Bryan has never left my life at any point during this time, and he’s had two children in the period of the campaign.”
Avantium’s vision is one where the chemical and materials industries will closely collaborate with farmers to build new supply chains and use all parts of the plants in a sustainable way for making food and materials. To make this a reality, the company recently announced the creation of a joint venture with Cosun Beet Company, a co-op of 9,000 farmers, to build a plant-based glycol flagship plant, using sugar beet as feedstock.
The journey towards a circular economy is one that will involve many players. Collaboration between experts and companies with shared environmental values is the only way to succeed and ensure that the technology is not only developed, but also made accessible to consumers.
“Our new partnerships are exciting points of validation,” Van Aken says. “They demonstrate the commercial potential of PEF.”
Avantium has developed their solutions in partnerships with a number of brands, such as Coca-Cola, Danone and Carlsberg. For example, the company is working alongside beer brewer Carlsberg in the development of PEF-based packaging of beer, such as the Green Fibre Bottle.
As consumers’ behaviours change to demand more sustainable products, countries around the world are imposing measures and setting deadlines to reduce plastics and carbon footprint. COP26 is part of this story, but not the whole picture.
“We are seeing signs of positive change,” Van Aken says. “Small steps are being taken, such as events like COP26, but leaders need to understand we need radical change to hit the proposed timelines. Ultimately, we are running out of time.
“The appetite for change provides opportunities for technologies like ours to be successful. Governments play a key role in enacting change, but also industry and consumers play a key role. We are in the middle of a decisive shift, whereby in the past we have moved far too slowly away from dependence on fossil fuels, and there has been a significant push for recycling and renewable energy programmes in the past. Now, more emphasis and investment need to be placed into the renewable chemistry sector to commercialise these breakthrough technologies and transition into a circular, sustainable economy.”
Step by step, companies such as Avantium are taking the lead in making that change. Looking towards the future, Van Aken is excited about the development of Avantium’s “first-of-a-kind” flagship plant, which will be built in the Netherlands and is set to open in 2023, with the goal of sending the first PEF products to market in 2024. Moreover, the company is also excited about developing its other technologies.
All of these developments will be fundamental if Avantium is to realise its pledge: a fossil-free chemical industry by 2050.
“The time to act is now,” Van Aken says. “We’re seeing great progress as governments and the private sector set net-zero targets and look for greener alternatives for our everyday products. The next generations are rightfully demanding that we put our energy into taking more drastic actions to ensure that we cut our carbon emissions and reduce plastic waste. By developing, scaling and adopting sustainable technologies, working to form new supply chains and adopting circular practices, we stand a better chance of reducing plastic pollution and achieving a greener future”
“Decades of short-term thinking is causing irreversible consequences to our environment. We must adopt a long-term view – investment in innovation and sustainability is needed now for the essential benefits to be felt in the future.”