
It might seem strange to hear it but starting out as a DJ set me up for a career in business.
Back when DJing involved spinning vinyl records that you’d lugged into the venue and not just turning up with a laptop and pressing buttons, I bought myself a set of decks and was playing at various parties five nights a week. Although I was supposedly doing a building diploma at the same time and the late nights meant that my studying wasn’t perhaps as focused as it could have been, I was learning about the elements of running a business such as local marketing and managing my accounts.
When I left college and transitioned away from the party scene, I took up work as a jobbing builder and developed my knowledge and confidence with a range of projects, but it was from the experience of having operated a disco business that I understood the parameters of running a small company. That foundation enabled me to grow from being a sole trader to walking into the local bank manager’s office – back when bank managers had offices and you could talk them through your business plan – and getting funding to buy a property for renovation. That was where Gusto Group began; over 30 years and countless projects ago.
Construction has continued to be at the heart of the Group – through Gusto Construction – and along the way we’ve done some soul searching as to the direction of travel for the business amidst the standards across the wider industry.
What amazes me most about the changes in construction in the last 30 years is, in fact, the lack of them. While other sectors have innovated at staggering speeds, such that technology has come on leaps and bounds, the processes and ways of working in the building industry remain largely the same as they were three decades ago. Concrete is still the material of choice, and the second most used material on the planet – after water – to the tune of about 30 billion tonnes each year. This relies on the manufacture of about four billion tonnes of cement each year, producing an unfathomable 2.5 gigatonnes – that’s 2.5 trillion kilos – of CO2.
And there’s no sign of this slowing, despite the increasingly apparent issues our planet is facing amid the mounting climate crisis. Unfortunately, claims that these figures could be decreased by 2050 (by the likes of McKinsey) aren’t doing enough to solve the crisis that we are already facing now.
The simple reason for the sector failing to innovate is the lack of incentive to do so.
As things stand, developers are held to woefully low standards of basic building regulations and there are minimal drivers to go above and beyond these. We all need somewhere to live, of course, and here in the UK the new Labour government has pledged to ‘get Britain building again – starting with one and a half million new homes across the country within five years’. But, with minimal incentives from the government for companies to do any more than pay lip-service to sustainability commitments, why would developers bother?
All companies want to make money, that’s a given, and, with the margins as low as they are in construction, any way of cutting costs is good in most developers’ eyes. Answering the ‘why would developers bother?’ question, then, comes down to the individual companies and their raison d’être.
It comes back to the soul searching I mentioned. And it comes down to differentiating between value and values.
While the PLCs are largely out purely for the monetary value that can be derived from throwing up houses and doing so to the minimum requirements, the onus falls on the smaller housing builders – Gusto Construction included – to take the lead on incorporating technologies that can push us towards zero carbon targets.
At Gusto we believe that technological innovation is a must-have, not a nice-to-have, across the construction space if we’re to make any headway towards the transition to net zero. And, while the margins are tight, as mentioned, we’ve been finding ways of making innovations commercially viable since our first project built to what I’d call ‘eco excellence’ standards back in 1996/7. Back then we introduced 150mm wall cavities, allowing for three times as much insulation as minimum standards; we put in rainwater harvesting systems; we installed solar thermal water heating; we were one of the first companies to do any form of air testing, to check for air tightness and whether the homes were losing heat.
We didn’t get any external funding for that project so it had to work commercially and, although it was a bit of a punt because the homes cost us more to build, it facilitated the opportunity to look at other materials that we could invest in. Since then, we’ve done a variety of different types of developments and, when a project allows us to do something a bit more experimental, or we can negotiate a relaxation of affordable housing contributions or planning obligations, the result is always residents feeling like they’re a part of something.
That sense of community is something we should all be aspiring to because it forces us to go beyond the finances of house building; the value becomes about improving people’s lives and the knock-on positive impact on the planet. Add in infrared panel heating systems that remove the need for air-source heat pumps because the energy requirement is minimal; power diverters that take solar-generated energy straight into the hot water cylinder, so you’re using your hot water cylinder as your energy store; heat recovery ventilation systems; use of natural materials like hemp that can absorb more carbon per hectare than any forest; and you have what our owners have described as “the next generation of eco homes”.
These ethics sit at the heart of our business as a sustainable group of companies and have been the drivers of going through the process of gaining B Corp certification. This ensures we are continually holding ourselves to higher standards across a range of metrics, both within our own organisations but also across our supply chain. It extends to planet, people and community, and we should aspire to make a connection between the three.
The Labour government has talked the talk of ending ‘the climate and energy chaos’ but hasn’t yet walked the walk by putting the appropriate measures in place. Policies that incentivise companies to cut their carbon emissions – or penalise them for not doing so, like a tax on carbon intensive materials – would go some way to levelling the playing field for those that are trying to make a difference but are struggling to do so because of the margins we’ve discussed.
Another option would be to insist that councils only partner with businesses that can prove their green credentials (for example through the B Corp movement or membership to the Association for Environment Conscious Building). If a company was unable to win business because it wasn’t operating according to stricter, more environmentally friendly processes, you’d hope it would strive to do better, leading to improvements in sustainable practices across the sector.
When US Senator Paul Wellstone gave a speech to the Sheet Metal Workers Union in 1999, he said, “We all do better when we all do better.” We’re trying to do better but we need others to follow suit and see the value of sustainability in shaping the future of the sector.
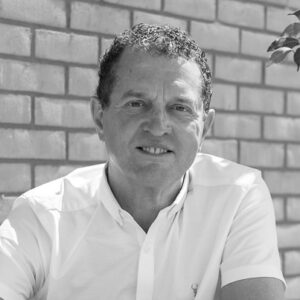
Steff Wright
Steff Wright is Chairman of Gusto Group.